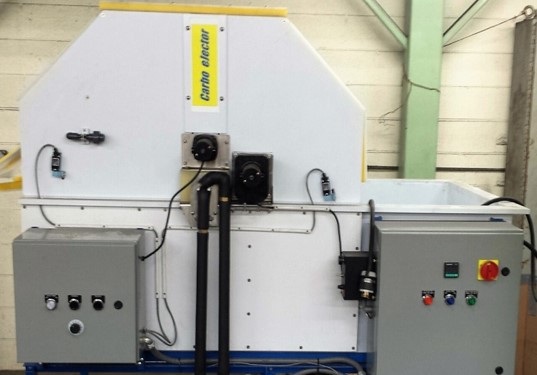
Innovative System for Carbonate Removal from Plating Baths
Continuous “ Flow Through” design with high rate of Carbonate removal.
Design flow of 1+ Gal/Min.
(actual flow of over 2 Gal/Min proved successful)
No more small batch treatments with long processing time.
- Efficient, high BTU output LOW TEMP refrigeration with modern screw type compressor.
- Option of liquid or air cooled condenser unit.
- Precisely controlled treatment temperature with wider range of low temperatures if required.
- Low volume of plating bath(~60 Gal) contained in the treatment tank.
- Drum crystallization method with ejection of portion of free flowing carbonate slush ~every 1.5 min.
-
Carbo eJector Features and Operating Principles
The Carbo eJector TM units are designed to efficiently and economically remove excess carbonates or other type salts from plating baths and various industrial process solutions.
The Principle operation of the Carbo eJector TM units is based upon inducing crystallization of accumulated undesired salt. This is accomplished by lowering the solution temperature below the compound’s saturation point, which then drops out it’s excess carbonate (salt) from the solution to form a small crystalized slush.
Examples of Salts other than Sodium Carbonate are: Ferrous Chloride, Ferrous Sulfate, Aluminum Sulfate, Aluminum Hydroxide, etc. which are compounds with low solubility at lowered temperatures.
Typical industrial electrolytes and baths that the Carbo eJector TM can separate waste build up from include: Alkaline Zinc, Alkaline Zinc Nickel, Cyanide Zinc, Cyanide or Alkaline Copper, Anodizing Baths etc.
Carbo eJector TM units perform this treatment in an innovative manner by using a continuous *Flow Through Design at a rate of ~1 to 2 Gallons per minute of the cleaned bath through the Treatment Compartment. From here, formed Crystallized Slush contaminants are continuously and mechanically ejected from the plating solution in the Crystallization Compartment and in the next step, separated from the liquid by several possible methods with varied efficiency. 1.0) The simplest method being gravity filtration accomplished by the furnished filter bag totes. 2.0) The best possible separation being achieved by quick centrifugation or spin drying, with the possibility of returning the now cleaned solution back to the process tank potentially saving significant money and resources.
Please ask about those additional options if the volume of removed contaminant would offset the cost of treated bath or if the environmental requirements or concerns warrants such additional step.
- *Most competitors use the “batch method” of crystallization which is limited, time consuming and requires significant attention and monitoring compared to the Flow Thru design of the Carbo eJector TM.
MADE IN USA, easy access to spare parts